Integrating reading glasses into government supply chains is a formidable challenge faced by many Ministries of Health (MoH) and the eye care NGOs who are supporting them to achieve sustainable government-led delivery.
In this article, EYElliance shares our experiences in supporting the Ministry of Health in Liberia to integrate reading glasses into Liberia's community health supply chain —revealing both the successes and challenges we encountered on this journey.
Let's dive into the complexities of this integration and the unexpected lessons we learned along the way.
Understanding Liberia's Supply Chain
Liberia boasts a relatively well-established and functioning government supply chain, which is a significant asset in our mission. As in most contexts, the system is not without challenges—this therefore provides us with a practical opportunity to explore how integration can be achieved within a complex system.
Key players in the Ministry of Health (MOH) include the Supply Chain Management Unit (SCMU), Central Medicine Store (CMS), and supply chain focal points within the National Eye Health Program (NEHP) and Community Health Services Division (CHSD), which is responsible for leadership of Liberia’s National Community Health Program (NCHP), including provision of vision screenings and reading glasses by Liberia's Community Health Assistants (CHAs).
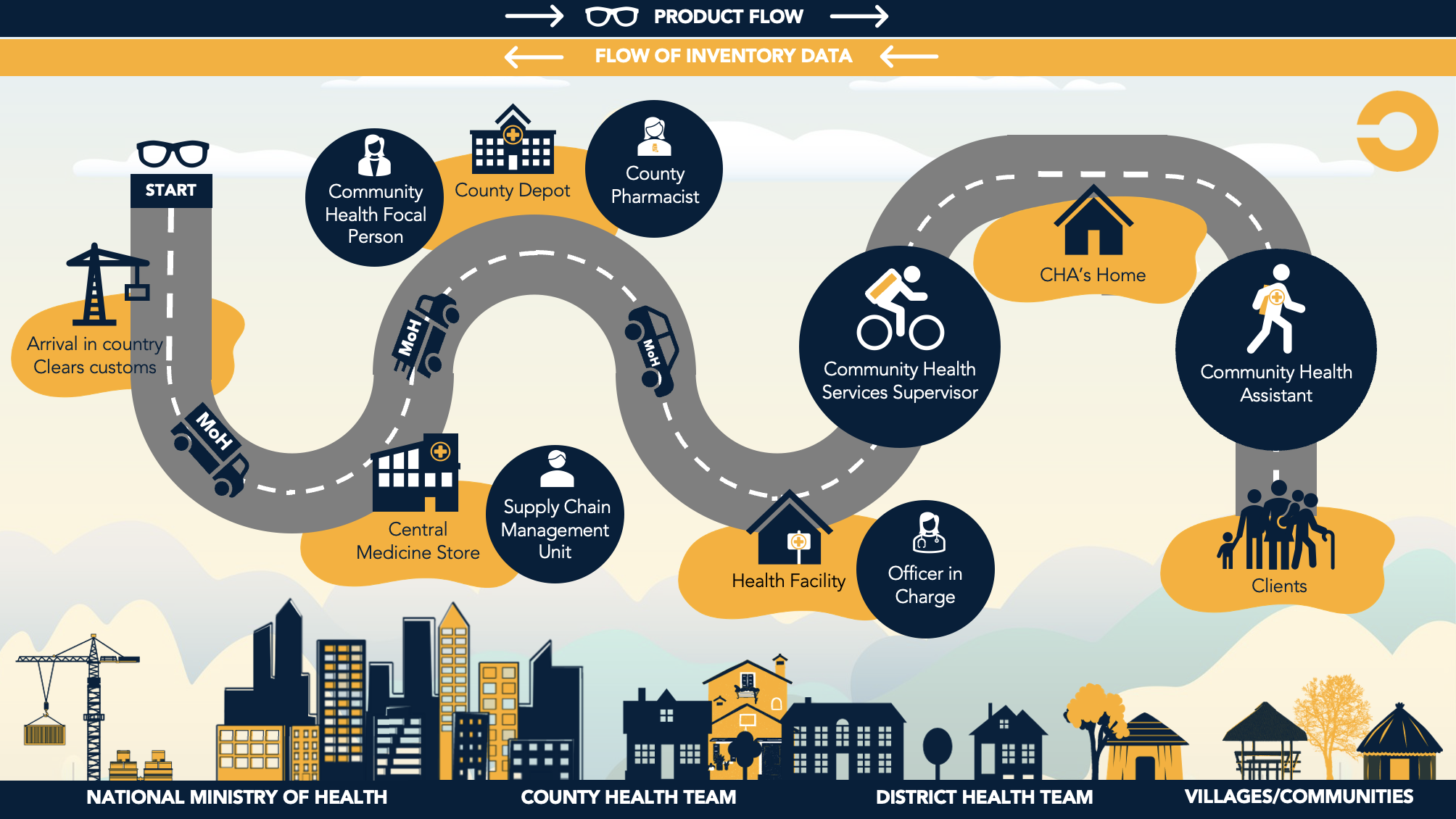
In an idealized scenario, reading glasses are seamlessly integrated into the existing supply chain, moving from the Central Medicine Store to each county and then down to community health workers via their respective health facilities. However, achieving this ideal flow presented both EYElliance and Liberia’s Ministry of Health with numerous challenges and lessons.
Learning #1: ‘Making It Work’ Via Collaborative System Actors
One of our key takeaways from this integration journey is the necessity of adapting to the system's realities. Despite the fact that Liberia has a well-designed supply chain on paper, we encountered challenges in practice. Our shared goal was to avoid creating parallel systems just to achieve pilot outcomes; instead, together with the MOH, we designed for inclusion of glasses into the supply chain from the beginning of the program.
This is where the importance of relationship building with key individuals within the medical supply chain system played an important role. The identification of unique systems actors (or focal points) capable of facilitating teamwork across divisions at the national level was critical in engaging and promoting collaboration between the National Eye Health Program, Supply Chain Management Unit and Community Health Services Division—three divisions which had to collaborate and align in order for the program to be successful.
The necessary focal point roles already existed at the Supply Chain Management Unit and Community Health Services Division, but there was no supply chain focal point at the National Eye Health Program at the start of our collaboration. Typically, supply chain focal points for specific service delivery areas, such as eye health, malaria control, or childhood immunization, provide the Supply Chain Management Unit and Community Health Services Division with technical guidance on the commodities needed for provision of that program’s services - in this case, reading glasses that Liberia’s CHWs would provide to their clients. The appointment of a national supply chain focal point within the National Eye Health Program and his collaboration with us and his counterparts at the Supply Chain Management Unit and Community Health Services Division, bridged gaps in the crucial network of collaboration between divisions.
Collaboration between these focal points created a real-time, nuanced understanding of system bottlenecks and challenges, informed by local context. This allowed us to navigate the system and identify which wins were important for integration.
For example, this collaboration ensured the integration of reading glasses into the Electronic Logistics Management Information System (eLMIS): crucial for recording inventory data, guiding planning and decision-making for quantification, and forecasting for resupply—a win for normalizing reading glasses as a standard health commodity for CHWs in Liberia.
Finding and connecting with key, collaborative actors within the system can be a game-changer in achieving functional integration.
Learning #2: 10,000 Stickers
For the pilot, EYElliance received a donation of ~10,000 pairs of reading glasses that included over 50 different combinations of powers, models, and styles. While this level of variety gave clients more selection in their choice of reading glasses, EYElliance and our Ministry counterparts faced the daunting task of figuring out how to manage this range of products within the existing system.
To inform their manufacturing, the supplier for the donation tracks each of these combinations of power, model, and style individually. To do this, they use a labeling system that treats each combination as a separate “Stock Keeping Unit” (SKU). However the introduction of these 50+ new SKUs into Liberia’s supply chain system would have nearly tripled the number of products being tracked for community health services; this level of tracking would have quickly overwhelmed Liberia’s community health supply chain by increasing the complexity and workload for those responsible for stock-taking, tracking, dispensing, and restocking both upstream and downstream in the supply chain.
To complicate things further, the manufacturer’s SKUs are printed as a complex series of numbers and letters printed in tiny text on the inside of the glasses’ earpieces. It would not have been feasible to train all supply chain, community health, and eye health staff at the national, county, district, health facility, and community level in the nuances of decoding the supplier’s labeling system, nor to expect them to be able to read the small printed text on each pair of glasses when working with inventory sizes reaching into the tens of thousands.
Clearly another approach was needed. Liberia needed its own, fit-for-purpose SKU system that balanced simplicity and tracking with variety and dignity of choice.
This system also needed to be stable and have continuity: able to adapt to changes in the supply of powers, models, and styles, without the need to constantly re-do documentation or processes.
To simplify stock management and prevent SKU proliferation, we collaborated with the MOH and CMS staff to test a system that reduced over 50 variations to just nine options, based on three powers and three models. To make it easier for downstream staff and CHWs to quickly identify each of these nine SKUs, without needing to look back at the tiny text on the frame, the team introduced a sticker system whereby each pair of glasses would have one sticker indicating the power and another indicating the model. Although the glasses already came with “power stickers” on the lenses, the team at the central level needed to affix an additional sticker for the model. Putting this into practice required printing and adhering ~10,000 relabelling stickers—a massive effort, but one which paid off in the long run.
With one quick look, staff at any level of the supply chain could quickly identify the SKU of any pair of reading glasses within the system.
Based on learnings from the pilot, EYElliance and the Ministry of Health are now collaborating to further simplify strategies for stock management of reading glasses within the National Community Health Program.
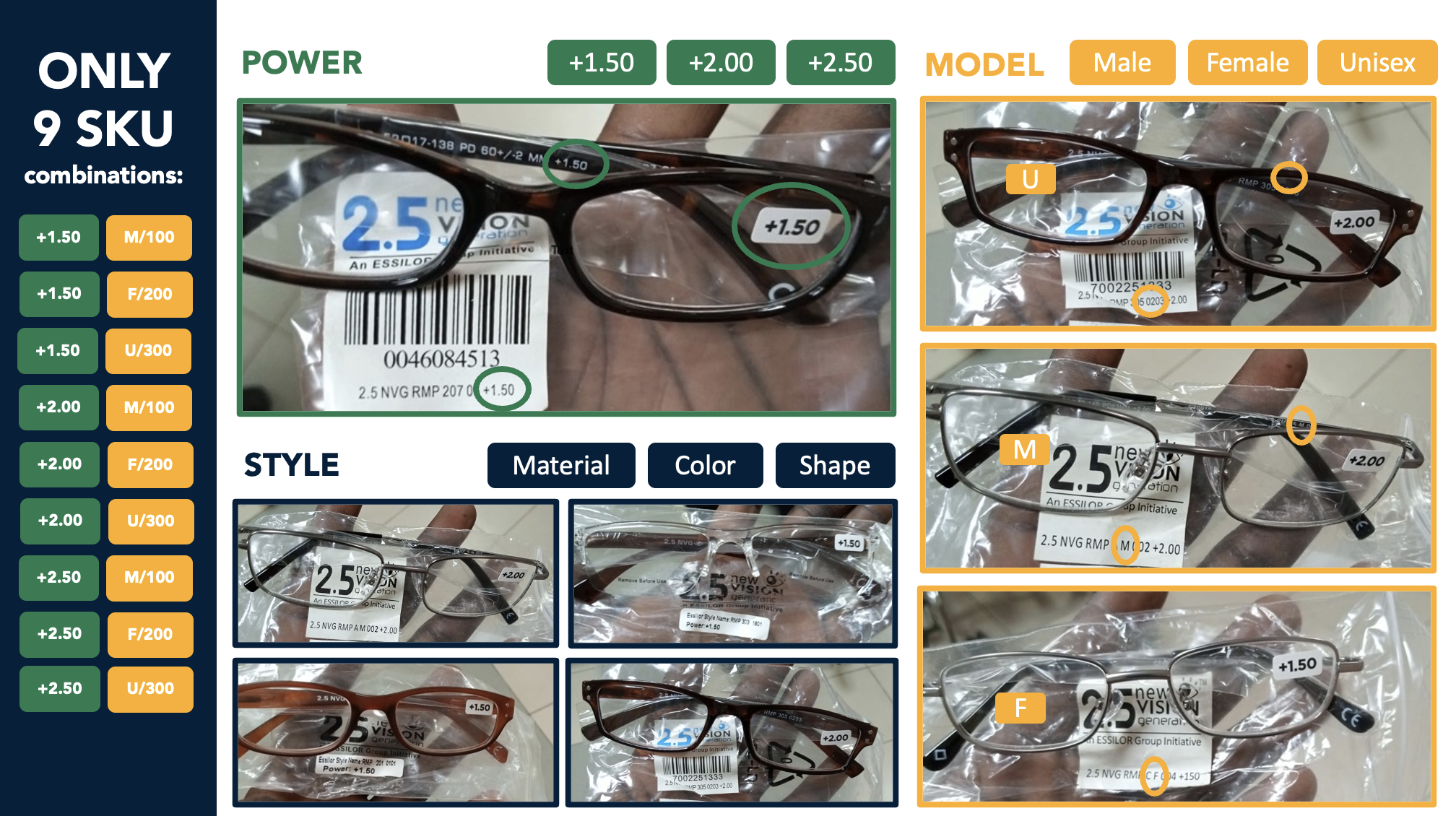
Learning #3: Training The Human Resources That Power The System
Simplification of SKUs within the supply chain is essential, but not sufficient for integrating eyeglasses as a normalized government health system commodity. You also need to train people. Existing human resources within the Liberian government health supply chain are the conduit by which all aspects of the program are executed and sustainable long-term.
The health supply chain is made up of thousands of primary health workers as well as MoH administrators working at each level of the system. The task of full integration means that all of these personnel need to be sufficiently trained to create a shared understanding of the system, increase efficiencies and identify areas where other resources and functions within the system can be fully leveraged.
Training for CHAs and CHSSs extended beyond service delivery activities like vision screenings and eyeglasses dispensing—it was crucial to integrate supply chain training into the core community eye health training sessions for these cadres. It was also imperative to train the health system administrators responsible for supply chain functions that ensure the flow of inventory to CHSSs and CHAs.
For CHAs, the training focused on specific considerations for managing reading glasses as a product. For example, how to handle eyeglasses and prevent breakage. CHAs were also trained on tracking their consumption of reading glasses along with commodities for other service delivery areas.
Training for CHSSs covered CHA training topics but also included additional sessions focused on how to interpret and understand the simplified fit-for-purpose SKU inventory system and how to restock and requisition reading glasses using updated versions of existing supply chain forms.
Training for national, county and other administrators, covered the the core aspects of CHA and CHSS training, but additionally, they received orientation on conducting initial product inventory, which included translating manufacturer SKUs into Liberia's simplified fit-for-purpose SKU system. Administrators were also trained on estimating and fulfilling supply needs, and planning for distribution of reading glasses alongside other National Community Health Program commodities.
Ensuring staff were effectively trained increased the efficacy of the integration and positioned the program for government ownership and execution.
The Way Forward
Integrating eyeglasses into Liberia's government supply chain was not without its challenges and surprises. Our journey taught us valuable lessons about adapting to nuanced systems. This included the importance of relationship building with key individuals who can foster collaboration, and designing fit-for-purpose stock-keeping processes. We also learned about equipping human resources so that they can ensure smooth integration and fully leverage other resources and functions within the system. While Liberia's supply chain may serve as a model for some supply chain components, it also highlights the value of innovation and flexibility when integrating eyeglasses into various systems worldwide.
As we continue to work on creating a world with equitable access to eyeglasses, we encourage others to share their experiences and collaborate on finding solutions to similar challenges. Together, we can improve the lives of countless individuals by providing them with the gift of clear vision.